The home stretch.
- owcogolf
- Sep 13, 2023
- 3 min read
Making putters is hard. Honestly, it is. Before we got into this business, I always wondered why milled putters were expensive, why there was always a waiting list and why it took a while to have a custom putter maker build me a putter. I mean, just cut it out of metal and add some paint... not that hard.
I now know.
Just a few things come to mind: purchasing the metal, rough cutting it to ensure we aren't wasting any of that expensive silver stuff, figuring out the programming, buying and setting up vices to hold the metal during the different milling phases, changing positions of the metal, overseeing the milling process so a broken end mill doesn't ruin a head, the list goes on and on.
With that being said, our first prototypes (the two putters you probably have seen throughout this site and our social media posts) were very good. Almost every detail we designed was implemented correctly and for our first milled piece, we were blown away.
Being perfectionists and knowing the EXACT look we hoped to achieve, spending more time with those prototypes enforced that we needed to make a few changes. These changes were strictly aesthetic, nothing that would change the performance of the putter, but isn't looks 98% of the reason you decided to purchase one putter instead of another? We needed it to be perfect.
So why did a few little tweaks take so long? Let me go on a tangent and explain and add some transparency.
Nick and I designed, measured, sketched, photoshopped and mocked up every aspect of this putter. Where bevels should be, how heavy should they be, chamfers, the face mill pattern, the look of the sole ... every aspect. Unfortunately, we aren't machinists, so turning those ideas into reality wasn't something we could do quickly, or without a huge learning curve. Thankfully Nick's family owns a machine shop in Massachusetts and his father is a master machinist. We had to convey every design aspect to him to turn that into CAD drawings, and then into G-code. Of course this wasn't his full time job and he didn't have a lot of free time to spend with us... and is why it took 6 or so months for us to get our first prototypes. Little by little, day by day.
There was a lot of frustration, difficulty getting on the same page, trying to convince him we could do something he didn't think was possible. Shop time was necessary, yet there wasn't much of that available, as his daily jobs kept him 100% busy, actually -- more like 120%.
When we said we had some final tweaks before our production run, I'm not sure any of us knew exactly what that meant as far as how much time, effort and cost that would result in, but that's what we've been working on (among other things) since we showed off the first prototypes.
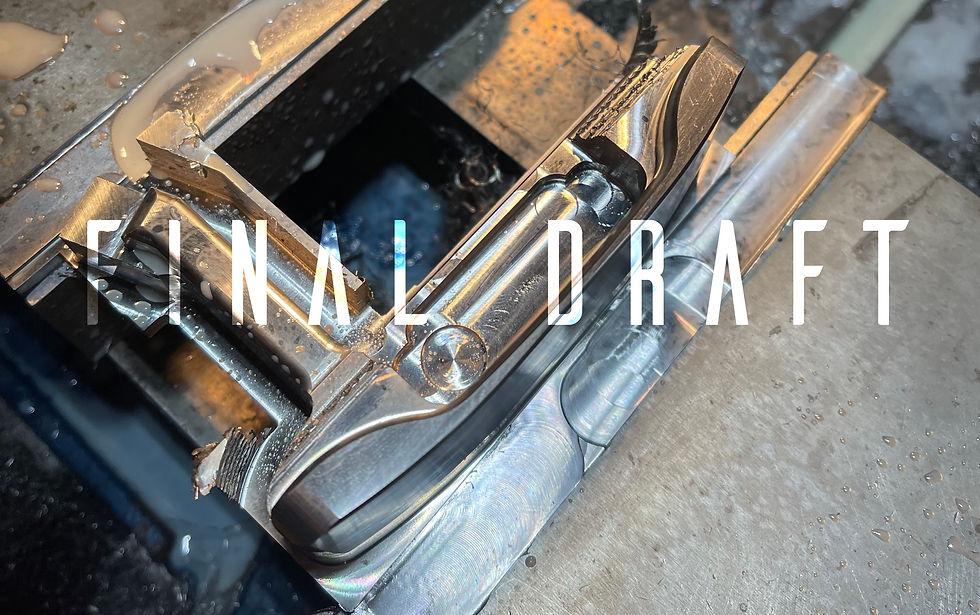
Today we're extremely close. What you see above is the final design of the rear of the putter. I won't go into too many details as I'd like the final reveal to be a bit of a surprise (don't worry, it's nothing dramatic), but we feel that we nailed the overall look, focused on the details others leave out and have one hell of a good lucking flatstick.
Currently, we're milling the backs of each of the putters in the first batch. There originally was 12 putters planned, but we ended up getting him to agree to 16. 10 have been preordered, two are going to be used for prototyping some interesting ideas and we're going to build the remaining ones out with some ideas Nick and I have been throwing around. Those will be for sale in the not-so-distant future, so stay tuned.
The majority of the milling work and time is spent on the back of the putter, the front and top is much quicker. We have a few tweaks being made to those sides as well, but nothing as intense as the rear. Once the rear milling is done for all putters, we'll implement the changes to the other sides, assuming all is good we'll provide the green light to complete the putter heads.
Once the heads are complete, we'll be reaching out to everyone who preordered to complete their final payment and sign off on their final design. We'll then add in the sight lines and custom stamping, provide our stardust finishing process then paint fill everything and let it cure. The next thing after that is for everyone to keep tabs on their email, as shipping notices will go out.
We're in the home stretch here, we thank everyone for their patience and support, we think you're going to love the changes we've made and we promise the wait will be worth it when you get one of our putters into your hands.
<3 Pete
Comments